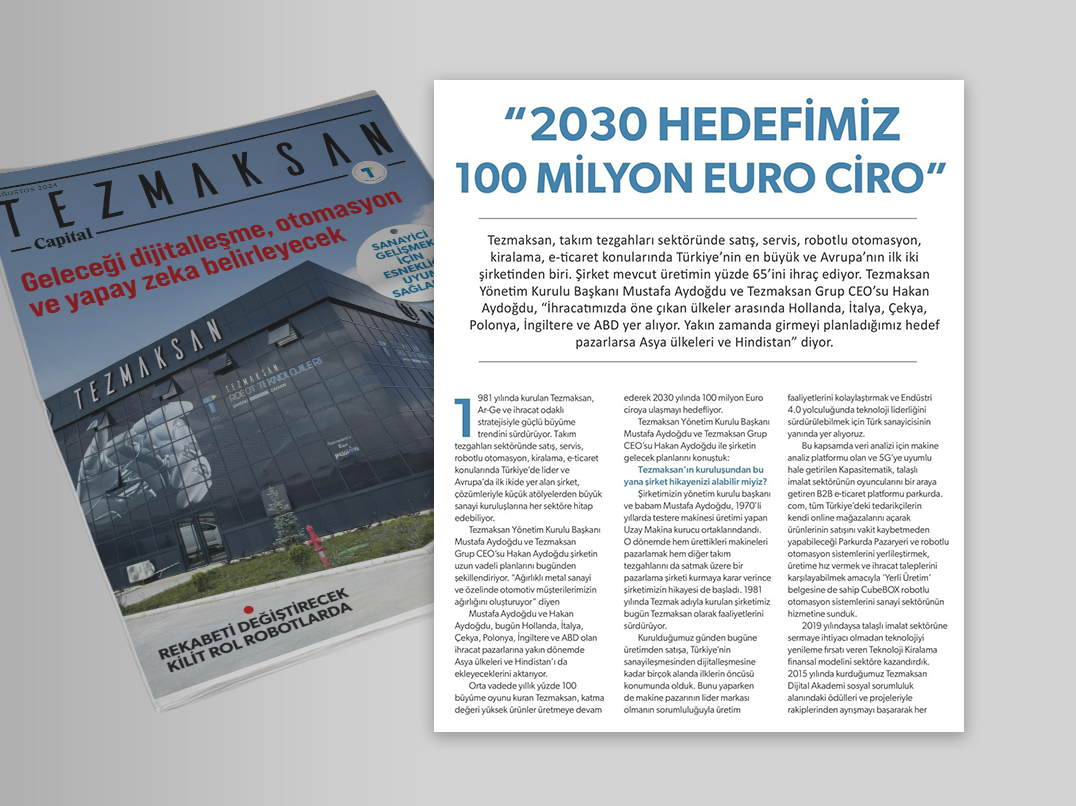
Our 2030 Goal 100 Million Euros In Revenue
Tezmaksan, led by CEO Hakan Aydoğdu, is the largest company in Turkey and one of the top two in Europe in sales, service, robotic automation, leasing, and e-commerce in the machine tool sector. The company exports 65% of its current production. Tezmaksan Chairman Mustafa Aydoğdu and CEO Hakan Aydoğdu state, "The leading countries in our exports are the Netherlands, Italy, the Czech Republic, Poland, the UK, and the USA. In the near future, our target markets are Asian countries and India."
Founded in 1981, Tezmaksan continues its strong growth trend with an R&D and export-focused strategy. The company leads Turkey and ranks among the top two in Europe in sales, service, robotic automation, leasing, and e-commerce in the machine tool sector, offering solutions to sectors ranging from small workshops to large industrial enterprises. Tezmaksan Chairman Mustafa Aydoğdu and CEO Hakan Aydoğdu are shaping the company's long-term plans today. They state, "Our customers are mainly from the metal industry, specifically the automotive sector." They plan to expand the export markets, currently including the Netherlands, Italy, the Czech Republic, Poland, the UK, and the USA, to Asian countries and India shortly. Tezmaksan, aiming for an annual growth of 100% in the medium term, targets reaching a turnover of 100 million Euros in 2030 by continuing to produce high-value-added products. We discussed the company's future plans with Tezmaksan Chairman Mustafa Aydoğdu and CEO Hakan Aydoğdu:
Can we hear the story of your company since its establishment?
Our company’s chairman and my father, Mustafa Aydoğdu, was a founding partner of Uzay Makina, which produced saw machines in the 1970s. When they decided to establish a marketing company to market the machines they produced and sell other machine tools, our company’s story began. Founded in 1981 under the name Tezmak, our company continues its operations today as Tezmaksan. Since our founding, we have been pioneers in many areas, from production to sales and industrialization to digitalization in Turkey. In doing so, we have been standing by Turkish industrialists to facilitate production activities and maintain technological leadership on the journey of Industry 4.0 as the leading brand in the machine market. In this context, we have launched CubeBOX robotic automation systems, which have a 'Local Production' certificate, to localize robotic automation systems, accelerate production, and meet export demands, as well as the Capacitymatic machine analysis platform compatible with 5G for data analysis, the B2B e-commerce platform parkurda.com bringing together players in the machining industry, and the Parkurda Marketplace where suppliers across Turkey can open their online stores and sell their products without delay.
In 2019, we introduced the Technology Leasing financial model to the machining industry, offering the opportunity to upgrade technology without capital needs. Established in 2015, Tezmaksan Digital Academy continues to be a pioneer with its awards and projects in social responsibility, distinguishing itself from competitors.
What were the significant milestones from 1981 to the present, and how did your company stand out?
Since our establishment, important milestones include the free trade moves of the 80s, corporate investments of the 90s, and the information age of the 2000s, which were parallel to our initiatives that led our industry. Our technology and innovation investments, which gained importance after the 2010s with Industry 4.0, followed this. We reaped the rewards of our foresight and decisions on automation during the pandemic. In our digital transformation journey, we have employed local engineers and software specialists. We accelerated our technology and innovation investments after 2010, fulfilling the requirements of digital transformation. During our journey, we have not only shaped our adventure with our investments and innovative approach but also pioneered many products that support production and increase global competitiveness in Turkish industry. While doing so, we have been advocating 'Let’s Produce' to the entire industry because the changing era also alters the criteria for production. As an ever-updating and forward-looking institution, we have positioned ourselves as an entity that can analyze robotization, delivering robotic projects, and establishing an ecosystem where thousands of sector representatives meet. We are a technology company providing 360-degree service, offering rental services for robotic automation consultancy and transformation, real-time monitoring of factories, machines, and production, while providing skilled labor support and other services. In which markets do you stand out, especially?
We are the largest company in Turkey and one of the top two in Europe in sales, service, robotic automation, leasing, and e-commerce in the machine tool sector. Tezmaksan's knowledge-based solutions can serve every sector, from small workshops to large industrial enterprises, from automotive to aerospace, health, logistics, and warehousing. However, with familiarity with robotic automation systems and the emphasis on productivity and quality indicators, our customers are primarily from the metal industry, specifically the automotive sector.
What has been prominent in your growth in recent years?
Exporting the CubeBOX robotic automation system, developed with years of experience and innovative work, and its new models to 40 countries on 4 continents has accelerated our growth journey. Currently, we export 65% of our production, with prominent countries being the Netherlands, Italy, the Czech Republic, Poland, the UK, and the USA. In the near future, our target markets are Asian countries and India.
What will be your growth strategy for the upcoming period?
We are planning our growth strategy for the upcoming period with a focus on R&D and exports. Keeping up with the transformation in the industry and always staying one step ahead is a priority we have valued for years. For this reason, we believe that today’s matter is not just producing but producing with value and profit, so we emphasize R&D activities. Our main concern from now on is to support our solution partners’ competitiveness, reduce production costs, and save them time. For this very reason, we have developed solutions by observing our solution partners' competitiveness in national and global markets and responding to their needs. As a result of all these efforts, we have created branded systems and applications.
What investments will bring you growth in the future?
We recently became the automation solution partner of the Germany-based EMAG company and are carrying out a robotic automation project of a 10-line facility at an automotive manufacturer in Kyrgyzstan. The acceptance process for three of the lines has been completed. All lines will be operational in 44 weeks.
What are your medium-term growth goals domestically and internationally?
We foresee an annual growth of 100% in the medium term. We believe we will achieve our goals by expanding our impact and increasing sales, especially in the European and American markets. In the long term, we aim to contribute to the economy by producing high-value-added products with our high-tech products and reaching a turnover of 100 million Euros in 2030.
What are the most important issues on your agenda?
Our agenda is mainly focused on keeping track of current events. We are making progress through studies on artificial intelligence, market shares, competitor analysis, and R&D.
PRODUCTION BY ROBOTS
"WE CHOSE SIVAS"
The Hacı Mustafa Aydoğdu Production Center, whose foundation we laid in May 2022 in the Sivas Nuri Demirağ Organized Industrial Zone and officially opened in June this year, is at the heart of our recent investments. Our choice of Sivas was based on administrative incentives, logistical advantages with easy access to Samsun and Mersin ports via railway lines, and other criteria. Here, thanks to a railway line suitable for 25-ton axle pressure reaching inside the factories, we will significantly lower our logistics costs. Moreover, we chose Sivas to move away from the congestion in the Marmara region and to contribute not only to Sivas but also to the region, in addition to the approach of potential disaster management.
INVESTMENTS
Our factory, where we have reached 15 million Euros in investment and 2.5 million Euros in construction costs, spans a current area of 14,450 square meters. It includes a wide range of products, from 8-axis turning centers manufactured for the first time in Turkey in Sivas to new-generation CNC models. Including training, learning, and commissioning processes, we have manufactured a total of 70 CubeBOX units in our factory since October 2023 with mass production. With increased capacity, we aim to increase this number to 150 by the end of the year. From next year, we plan to produce 300 CubeBOX units annually on a single-shift basis. Our factory’s production system is designed and implemented to be compatible with the dark factory concept under the headline of Industry 4.0, using lean production techniques based on value stream studies. We perform standard tasks with industrial robots and material flows in internal logistics through autonomous mobile robots (AMR).
DARK FACTORY
Currently, our factory employs 16 people, 3 of whom are white-collar and 13 are blue-collar workers. However, the important point here is that our factory is compatible with the concept of a "dark factory," and the majority of production is carried out by robots. Turkey’s annual CNC machine requirement is 5,000 machines. Our production target is 80% export. The average price of a machine is 80-90 thousand Euros, with the price range going from 40 thousand Euros to 4 million Euros. By continuing to produce high-value-added products with high-tech products, we will reach a turnover of 100 million Euros by 2030.
THE CRITICAL USE OF ARTIFICIAL INTELLIGENCE
TRANSFORMATION
The field of machine tools, which has experienced a rapid transformation with computer-controlled machines where machines make machines, has made investments in automation a necessity rather than a preference since the pandemic. This field continues its transformation as the first industrial sector to integrate artificial intelligence into the production process. Considering the main trends in the machine tools sector, the development of automation systems will be a strategic area for us. Machine tools are critical to producing everything from cars to household appliances. Thus, increasing efficiency and capacity in the machine tools sector has become imperative. In the upcoming period, our primary goal will be to improve automation capabilities and further develop our smart solutions to minimize downtime and errors, reduce energy consumption, and maximize quality and efficiency.
ARTIFICIAL INTELLIGENCE
As the digital transformation accelerates, manufacturers strive to produce more cost-effectively, quickly, and efficiently, making artificial intelligence-supported automation systems indispensable. With these technological developments, it has become possible to increase production flexibility and accuracy while reducing costs in machine tools. Integrating artificial intelligence into production processes ensures manufacturing industries are equipped with smart production techniques. This approach offers superior productivity, flexibility, and cost-effectiveness, compared to traditional production methods, by increasing speed, accuracy, and cost-effectiveness.
INDUSTRY 4.0
From automation systems to robotization, the industry 4.0 revolution facilitates production, and with the efficient use of human labor, time, and energy savings, it increases production capacity and quality. Robots integrated with artificial intelligence can analyze production lines, identify disruptions, and take preventive measures. Automation systems developed with artificial intelligence help minimize human errors and improve productivity. On the other hand, artificial intelligence-supported solutions in automation systems will open up opportunities for machine tool companies to improve processes, increase efficiency, and reduce costs. AI-powered solutions offer faster, more efficient, and accurate production possibilities, allowing manufacturers to stay competitive in the ever-evolving industrial landscape.